Wyoming 1998
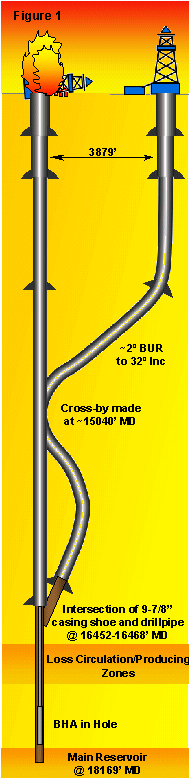
|
Problem: While
drilling into the top of the main reservoir, a loss circulation condition occurred which
ultimately resulted in the inability to progress further. The drillstring became plugged
and up to ~11800psi was present on the annulus of the 9-7/8 casing. It was decided
to put the well, which was producing ~40-45 MMcfpd at ~11000psi, on production and assess
intervention options. A relief well contingency plan was in place
shortly after the initial incident and identified critical issues, equipment and services.
After approximately six months of continuous production, the surface casing ruptured,
lifting the BOP stack, breaking several surface lines and resulted in a surface
flow/crater situation. Due to the close proximity of a nearby railway track, the dispersed gas flow was ignited for
safety reasons. The derrick and BOP stack were engulfed in flames, preventing any further
surface operations. Estimated surface flow was in excess of 70 MMcfpd. See Figure 1. |
Remedial Strategy: The relief well option was implemented without delay from a nearby well
drilling operation having a 3879 surface displacement. Estimated intervention time
was approximately 4 months to build, hold and drop profile well. The relief well would be planned
with a cross-by followed by a close proximity interval to accurately locate the blowout wellpath. After setting the
9-7/8 casing string at ~200 TVD above the target well 9-7/8 shoe, a
short interval would be drilled to intersect the blowout. A substantial kill pumping plant
would be necessary to successfully kill the uncontrolled well. A plugging operation would
commence immediately after killing to permanently plug the well. |
Special Services: John Wright Company (JWCO) was contracted to supervise the special
services required for the relief well intervention project. This would include
pre-planning and on-site supervision of directional drilling, surveying, kill operations
and casing detection. Specialists for directional drilling, borehole uncertainty and hydraulic simulations remained on site full time during the project. Vector
Magnetics, responsible for electromagnetic ranging, was coordinated through JWCO on this
project and worked together as one team. Well Flow Dynamics simulated various kill
scenarios for the kill operations, both surface and relief well kills. |
Challenges: The project
was complicated by the following:
- The surface displacement was high, caused by the decision to
redirect a vertical well currently being drilling adjacent to the blowout.
- MWD surveys existed, but no onsite QA/QC controls were
instituted.
- The kill/intersection point must be above the loss zones due
to casing string constraints/availability.
- Kill operation was influenced by the prolific blowout rate,
several loss/producing zones and the requirement to intersect at the 9-7/8 shoe
openhole interval
|
Results:
- The 'team concept' for special services was successfully and
efficiently utilized.
- The blowout well MWD surveys were found to be fairly
accurate and the well was found to be within 25 of the calculated position.
- The relief well crossed the blowout well at ~12 and
then dropped to vertical.
- During the cross-by losses caused the blowout well to bridge
and surface flow dropped dramatically.
- The surface operation required locating the wellhead and
cutting of the casing strings prior to setting up the snubbing unit and plugging the well.
- A milling and hydro-jetting operation severed the blowout
well drillpipe and no fluids were lost or gained, i.e. drillpipe was plugged.
- After extensive repairs to the platform
structure, field development was continued.
|