Pau France 1997
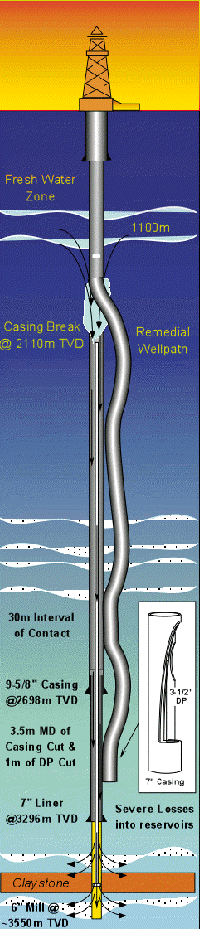
|
Problem: A workover
resulted in a collapsed casing situation with the BHA becoming stuck in a claystone
formation. Flow from a highly productive water zone at ~1100m TVD flowed into the two
underpressured production zones separated by the collapsed claystone formation. The
reservoirs were being "dump flooded" and the recoverable reservoir production
was dropping dramatically. Flow was suspected into both the DP and the DP x 7" casing
annulus. Fishing and other conventional methods and techniques resulted in several
unsuccessful and very costly attempts to plug and re-enter the well. The predicted
10,000m3/day rate of downward flow presented an unusual kill problem, requiring careful
analysis of all currently available mechanical plugging materials which would allow easy
and complete removal if the plugging attempt was unsuccessful. |
Remedial Strategy: The
flowing well was to be plugged by unconventional techniques. The remedial operation, which
utilized the existing wellhead, was planned to intersect the well in several intervals for
initially plugging and then for confirmation that the flow was halted. The remedial path
would begin at a sidetrack plug set atop the casing stub. After the setting of a 7"
casing string, a milling operation would establish hydraulic communication. Communication
must include milling of both the 3-1/2" DP and 7" casing to open all flowpaths.
The flow would be halted by plugging all flowpaths with CaCO3. CaCO3 could be acidized and
the flowpath re-opened if required. After evaluating the well conditions, a cement plug
would plug the well above the intersection point. The final P & A would not occur
until all evidence concluded that the well was permanently plugged. |
Special Services:
Applied Incident Management Inc (AIMI) was contracted to analyze intervention options,
prepare project engineering plans and to supervise and coordinate the special services.
On-site project engineering supervision of the directional drilling, surveying, casing
detection and milling operations were fundamental responsibilities for project success. |
Challenges: The project
was complicated by the following:
- Only low accuracy Dipmeter type surveys existed.
- Lost circulation would be present for the majority of the
drilling operations.
- Magnetic interference would require extensive use of
gyroscopic equipment.
- Additional zones of casing collapse were suspected and
required the intersection point below the 9-5/8" casing shoe.
- The kill & plugging program must not prevent other
control options if any operation failed.
- Drilling parallel and alongside existing casing without
surveys would require precise directional control and accurate casing detection techniques
|
Results:
- The existing wellhead was successfully utilized for the
remedial well.
- Several zones of collapsed casing were found with thermal
and magnetic data.
- A rate gyro was successfully used to orient drill with less
than 1º inclination.
- A ~30m 9-5/8" casing contact at ~80m above intersection
point was achieved.
- Communication established after milling 4m of 7" casing
and ~1m of 3-1/2" DP.
- Approximately 35 tonnes of CaCO3 were pumped to plug the
flow and a cement plug was placed in the casing and drillpipe above the intersection point
- A downhole video camera recorded the milling, killing and
pumping results and provided inconclusive intersection and plugging progress.
|