Middle East 1994
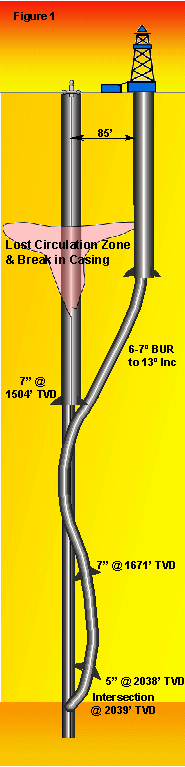
|
Problem: A production
well drilled in 1956 began to leak and charge a shallow aquifer. A workover rig identified
a hole in the 2 3/8" tubing and 7" casing created by this corrosive aquifer.
Communication with other wells in the field were established and sour gas was present in
several cellars. The well was blowing out underground and several attempts to P&A the
well using a workover rig were unsuccessful. |
Remedial Strategy:
Unconventional plugging techniques would be required for this blowing well. A remedial
operation with a relief well was planned to intersect the existing blowout wellbore at the
top of the reservoir. Hydraulic communication would be established and thixotropic light
weight cement circulated back to the casing break. The remedial well would be spudded at a
distance of approximately 85' from the problem well and well control measures would be
required when drilling through the shallow zone. |
Special Services: John
Wright Company (JWCO) was contracted to plan and supervise the drilling and special
services for this critical well. This would include pre-planning and on-site supervision
of all drilling operations, directional drilling, wellbore surveying, casing detection,
pumping, and cementing. Vector Magnetics, responsible for casing detection services, and
Well Flow Dynamics, responsible for kill simulations, worked together with the JWCO to
create a single team. |
Challenges: The project
was complicated by the following:
- There were no borehole surveys of any kind on the flowing
well
- Control of the pressured sour gas infiltrated aquifer would
require caution
- A relatively shallow target of unknown bottomhole location
would be difficult
- A modified casing program would be required to safely drill
to the reservoir
- Low formation strength and fluid loss problems required
special techniques.
|
Results:
- Team concept for special services was successfully and
efficiently utilized.
- The complex 3-D wellpath was modified continuously by
ranging results.
- Dogleg rates up to 12°/100ft were required, with an average
6-7°/100ft rate.
- The blowout well had ~4° inclination which was very
uncommon in the field.
- Drilling and flaring sour gas with a rotating head was
required in the top hole.
- The initial communication was at 1889 ft TVD with the relief
well and temporarily killed the blowout.
- Communication was immediately established upon entering the
reservoir.
- Light weight thixotropic cement was circulated to kill and
P&A the well.
|
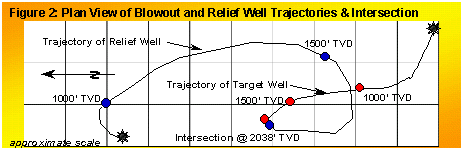 |