Lake Maracaibo
Venezuela, 1986
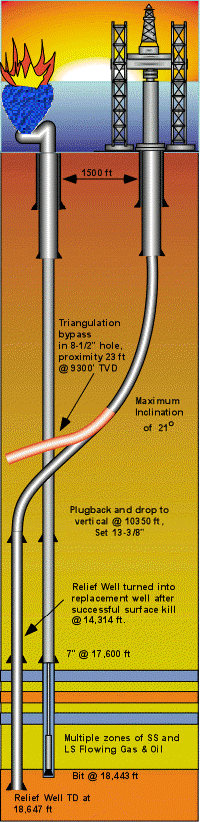
|
Problem: Operator had
drilled to TD at 18,443 ft. Mud weight was 15.7 ppg and became differentially stuck.
Reduced MW to 15.3 ppg and began to POOH to log when a swab kick was encountered 3500 ft
off bottom. While circulating out the kick a flange on the separator began to leak and
ignited. The fire destroyed the rig which collapsed into the lake pulling the 20
riser and all casing strings parallel to the lake bed. Flow of 40 MMscf/d gas and 7000
BOPD was estimated. The hydrocarbons burned on the lake surface. |
Remedial Strategy: Two
options were evaluated to stop the flow. The primary option would be attempted from the
surface. This included clearing the debris on the lake bottom, building a work platform
above the wellhead, preparing a subsea capping stack, preparing diverter lines, cutting
the casing strings and lowering the capping stack over the cut stub, diverting the flow,
rigging up a snubbing unit, snubbing pipe to a kill depth and kill and P & A the
blowout wellbore. If this option was unsuccessful a relief well started as a parallel
control option. |
Special Services: John Wright acted as an intersection unit leader for the directional
drilling contractor. Supervising borehole surveying, quality control, and defining
position uncertainty for drilled and proposed trajectories. |
Challenges: The project
was complicated by the following:
- Borehole position uncertainty was high.
- There were no suitable relief well rigs in Lake Maracaibo, a
jack-up rig had to be located in the region, refurbished, the legs partially removed to go
under the Maracaibo bridge, the legs reattached and towed to the south end of the Lake.
- The ability to precision directionally drill to intersection
would be extremely difficult and time consuming. In 1986 directional drilling motors and
MWD equipment were not designed for the expected high temperatures of the proposed
intersection depth of 17,600 ft of nearly 400 degrees F.
- Steerable motors were still in their infancy and were not
used on the project.
- Hole instability in the lower portion of the relief well
would require oil base mud complicating the electromagnetic ranging operation.
|
Results:
- A planning and execution team composed of the operator,
service companies and technical advisors from a major oil company were organized.
- A jack-up rig was located, refurbished and towed to
location.
- The triangulation bypass was successful in locating the
blowout casing at 9300 ft at a distance of +/- 23 away.
- The bypass section was plugged back and then dropped to
vertical and 13-3/8 casing set at +/- 10,350 ft.
- The 12-1/4 hole paralleled the blowout casing to
14,314 ft at a proximity of +/- 10 to 40 ft.
- When the blowout was controlled by Boots & Coots at the
surface the relief well was redirected as a replacement well to the blowout and was
ultimately drilled to a TD of 18,647 ft and became a producer.
|