Cook Inlet
Alaska 1988
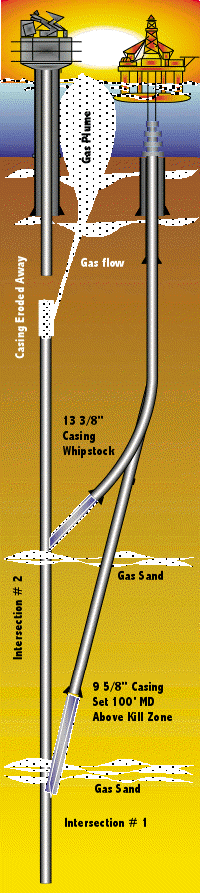
|
Problem: While
cementing the 13 3/8" casing, well control was lost on the annulus. Although
diverted, the situation turned into a blowout with a devastating fire which resulted in
severe platform damage. Ultimately the well bridged at the surface and the gas breached
the 20" casing, threatening the integrity of the platform and supercharging shallow
sands in the vicinity. A subsequent snubbing operation was unsuccessful due to the
presence of losses, shallow gas and rubble. |
Remedial Strategy: A
relief well was evaluated as the least risk intervention option and would be implemented
to stop the crossflow. A semi-submersible would be used due to the high tidal currents and
shallow gas hazards. Weak formation strength would not allow cement to be circulated from
the bottom of the blowout casing to the surface and therefore two targets would have to be
intersected. It was desired to use the same wellhead to avoid the double risk of spudding
with high tidal currents and shallow gas charging. A small team of specialists worked with
the operator to achieve these objectives. |
Special Services: John Wright acted as Intersection Unit Leader. Jim Woodruff
was Directional Drilling Unit Leader On-site project engineering supervision of the
directional drilling, surveying, casing detection and milling operations were fundamental
responsibilities for project success. |
Challenges: The project
was complicated by the following:
- Tidal currents of 7-8 knots created mooring
problems and spudding difficulties.
- Tidal height variations of 30' complicated
initial depth correlation.
- Shallow gas charging and a complete loss of
circulation zone below the 20" was expected and relief well planning included
appropriate options.
- Shallow targets and tides required anchoring
less than 400' from the platform.
- High dogleg severity rates would be required
in unconsolidated formations.
- Kill equipment and connection to wellhead
would be from a semi-submersible.
- Inability to monitor kill fluid and cement
placement on the crossflow.
- Approach angle required surface current
injection for electromagnetic ranging.
- Environmentally sensitive area mandated that
all operations must prevent spills
|
Results:
- Team concept involving industry specialists
and extensive pre-spud planning was instrumental to success.
- Semi was successfully moored adjacent to
platform despite high tidal currents.
- Semi was operated safely over a gas bubble
plume of over 200 ft in diameter.
- Extensive rig modifications were made for
diverting, pumping and safety.
- A 9 7/8" hole "shallow gas
exploration hole" drilled riserless 100' from spud location was suspended after it
blewout to the seabed.
- Sonar methods were successfully used to
monitor gas plume and tidal depth.
- Gas was diverted and controlled drilling
below the 20" due to loss of returns.
- Loss zone was ultimately controlled with
loss circulation materials and cement.
- Relief well trajectory was significantly
changed, as necessary, due to loss zones, directional responses and operational
requirements.
- Dogleg rates in excess of 12°/100' were
utilized to make intersections.
- Surface and downhole electromagnetic and
magnetostatic ranging was used to confirm intersection after first "lower"
cement job was completed.
- Second intersection was made using a 13
3/8" cased hole whipstock.
- Cement was successfully circulated into both
intersections after positive communication was established.
- After extensive repairs to the platform
structure, field development was continued.
|