California 1999
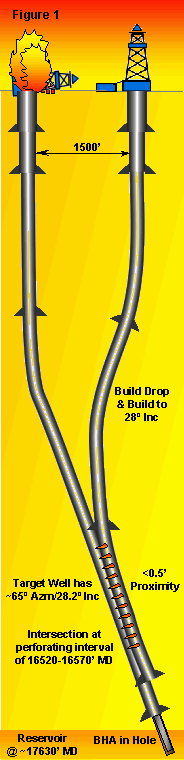
|
Problem: After setting a 7" liner string and drilling into the top of
the reservoir, a gain occurred which ultimately resulted in a surface blowout. The
estimated formation pressure was in excess of 15000psi with a BHT of ~350º F with
production rates estimated to be very high. A successful surface capping operation by
Boots and Coots IWC was achieved, followed by a snubbing operation to fish onto the
drillstring. After several unsuccessful surface kill attempts through the drillstring, it
was decided to put the well on production and further assess intervention options. An
underground blowout at ~2000-3000 was identified after further assessment with
hydraulic simulations and the presence of formation solids at surface. See Figure 1. |
Remedial Strategy: The relief well option commenced at a 1500 surface
displacement location. Estimated intervention time was ~ 4-6 months to drill the build,
drop build and hold profile well. The relief well was planned to intersect the blowout
well on the highside. After setting a 7" casing string at ~120 TVD above the
intersection point, a short interval would be drilled to parallel the blowout for
~50-90 After running a 5" scab liner to protect the wellbore and perforating
between the two wells, a kill operation followed by a plugging operation would plug the
well. Backup intersection methods included milling and hydra-jet. |
Special Services: John Wright Company (JWCO) was contracted to supervise the
intersection and assist in the overall design for the relief well project. Halliburton
Drilling Systems provided directional drilling supervision, MWD services and onsite
coordination. B&C and HOWCO Supervised the Kill Operation. Vector Magnetics provided
electromagnetic ranging services. Well Flow Dynamics provided simulation services for
various kill scenarios including surface kill options. |
Challenges: The project was complicated by the following criteria:
- The relief well was to intersect the blowout
and remain parallel with ~28º Inc.
- The relief well must achieve and maintain a
close proximity of <0.5 for 50-90 on the high side of the blowout 7"
liner string.
- A perforating operation must penetrate the
5" scab liner and the heavy walled 7" Q-125, 41ppf blowout casing string and
provide a very low pressure drop for the kill operation.
- Formation dips and strikes ranged from near
vertical to horizontal.
- Bottomhole conditions were near directional
equipment design limits at ~320 º F.
- High bottom hole pressure, inflow
performance and possible underground cross flow complicated kill operation planning.
|
Results:
- The Team Concept for special services was
successfully and efficiently utilized.
- The blowout well MWD surveys were found to
be within specifications and the well was found to be within ~65 of the calculated
position.
- A mud cooler/chiller was very successful in
lowering the circulating temperature.
- A highside intersection with ~50 of
<0.5 proximity was achieved. See Figure 2.
- After perforating, losses occurred and a
cement plug was pumped to a height of ~6000 TVD in the blowout well.
|
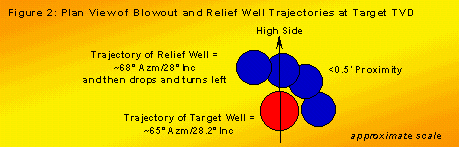 |